High Efficiency Electric Furnace For Melting Brass
By:Admin
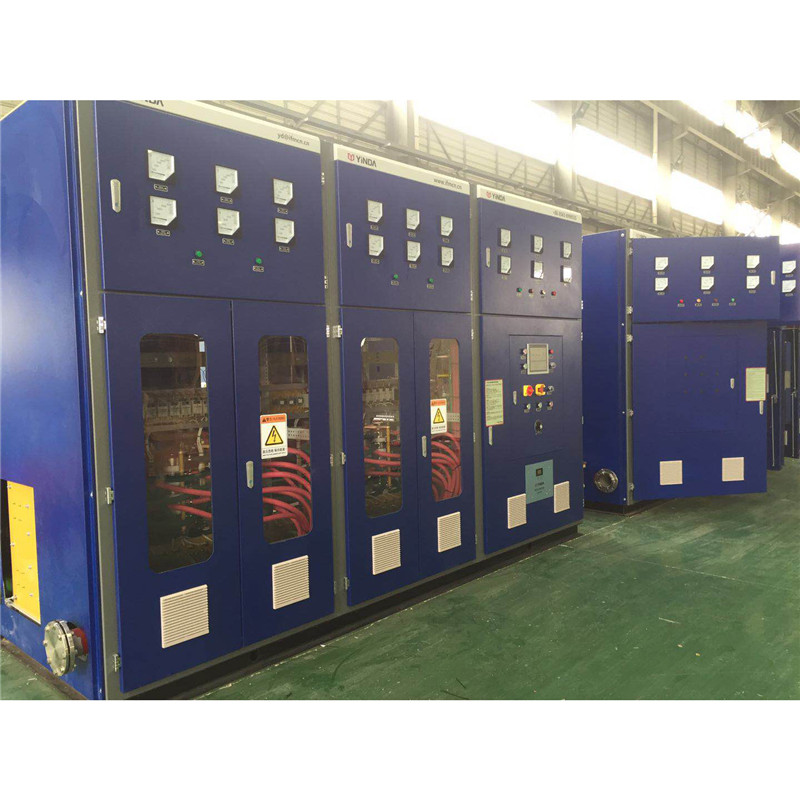
The foundry industry is undergoing a significant transformation with the introduction of modern electric furnace technology for melting brass. This new innovation is attributed to {Company}, a leading provider of advanced industrial equipment and solutions. The electric furnace is designed to offer superior performance, energy efficiency, and environmental sustainability compared to traditional methods of brass production.
{Company} has been at the forefront of developing innovative technologies for the foundry and metalworking industries for over three decades. With a commitment to continuous research and development, the company has established itself as a trusted partner for foundries seeking to improve their operational efficiency and product quality.
The newly introduced electric furnace for melting brass is a testament to {Company}'s dedication to driving progress in the industry. This cutting-edge furnace is equipped with state-of-the-art heating elements and temperature control systems that ensure precise and uniform melting of brass. Unlike conventional methods that rely on fossil fuels for heating, the electric furnace utilizes electricity, making it a more sustainable and cost-effective solution.
One of the key advantages of the electric furnace is its ability to achieve higher melting temperatures while maintaining excellent thermal efficiency. This translates to shorter melting cycles, increased productivity, and reduced energy consumption, ultimately leading to cost savings for foundries. Additionally, the electric furnace produces minimal emissions, contributing to a cleaner and safer working environment.
The implementation of the electric furnace for melting brass is especially beneficial for foundries aiming to enhance the quality and consistency of their brass products. The precise control of the melting process offered by the electric furnace results in a more uniform molten metal, which ultimately leads to higher-quality brass castings. This is particularly crucial for industries such as automotive, aerospace, and marine, where the performance and durability of brass components are paramount.
Furthermore, the electric furnace is designed with advanced safety features and user-friendly controls, ensuring ease of operation and maintenance. Foundry operators can rely on the electric furnace to deliver reliable performance and consistent results, thereby streamlining their production processes and improving overall operational efficiency.
In addition to the technical advancements, {Company} provides comprehensive support and technical assistance to foundries adopting the electric furnace for melting brass. This includes customization options, operator training, and ongoing maintenance services to ensure seamless integration and optimal performance of the equipment.
The introduction of the electric furnace for melting brass marks a significant milestone in the foundry industry, with the potential to revolutionize traditional brass production methods. {Company} is dedicated to driving this transformation and supporting foundries in their journey towards sustainable and efficient operations.
As the demand for high-quality brass components continues to grow across various industries, the electric furnace presents an opportunity for foundries to stay ahead of the competition and meet the evolving needs of their customers. With {Company}'s expertise and innovative solutions, foundries can embrace the future of brass production with confidence and optimism.
In conclusion, the electric furnace for melting brass introduced by {Company} represents a game-changing technology for the foundry industry. With its advanced capabilities, energy efficiency, and focus on quality, the electric furnace is poised to redefine the standards of brass production and drive the industry towards a more sustainable and competitive future. {Company} remains committed to empowering foundries with cutting-edge solutions, and the electric furnace is a testament to their unwavering dedication to innovation and progress.
Company News & Blog
Top-Rated Tilting Crucible Furnace Manufacturers in the Market
Best Tilting Crucible Furnace Factory Offers Top-Quality Products for Industrial UseFor many industries that require the use of metal casting, finding a reliable supplier of specialized equipment, such as tilting crucible furnaces, can be a challenge. However, the Best Tilting Crucible Furnace Factory prides itself on offering high-quality products for various industrial applications. As a leading manufacturer of tilting crucible furnaces, the factory has been serving the needs of industries in various sectors, including automotive, aerospace, and oil and gas. The company has been in operation for several years and is known for producing superior-quality furnaces that are reliable, efficient, and safe to operate.One of the unique aspects of the Best Tilting Crucible Furnace Factory is its innovative designs that focus on maximizing efficiency. The furnaces produced by the factory are designed with advanced control systems that regulate temperature and prevent overheating, thereby ensuring that the casting process is consistent and that the final product is of high quality. Additionally, the furnaces are built with durable materials that can withstand harsh industrial conditions and are environmentally friendly.The company's commitment to quality extends beyond its products and includes its customer service. The Best Tilting Crucible Furnace Factory has a team of experienced professionals who are dedicated to providing expert guidance and support to its clients. The factory's staff members are knowledgeable about the various applications of the furnaces produced by the factory and are always available to answer any questions or concerns their clients may have.The Best Tilting Crucible Furnace Factory also values safety and adheres to strict standards when it comes to safety protocols. The company is committed to providing a safe work environment for its employees and ensuring that its clients' operations are safe. The furnaces that the factory produces are designed to have minimal risk of accidents and hazards, and the company provides training and support to ensure that clients understand how to operate the furnaces safely.Moreover, the Best Tilting Crucible Furnace Factory is also known for its customization options. The company understands that each client has unique needs and preferences, and they offer tailored solutions to meet those needs. The company's team of experts works closely with clients to understand their specific requirements and design a customized furnace that meets those requirements.As part of the company's commitment to its clients, the Best Tilting Crucible Furnace Factory offers a comprehensive warranty program. Clients can rely on the warranty to cover any defects or faults in their furnaces during the agreed-upon period.In conclusion, the Best Tilting Crucible Furnace Factory offers exceptional products and services for various industrial applications. Its commitment to quality, efficiency, safety, and customer service has made it a reputable supplier of tilting crucible furnaces in the industry. Clients can trust the company's experts to provide tailored solutions that meet their specific requirements and deliver reliable products that are built to last.
Groundbreaking Discovery Unveils New Potential in Foundry Induction Technology
Title: Revolutionary Induction Technology Poised to Revamp Foundry IndustryIntroduction:In today's rapidly advancing industrial landscape, innovation and technological advancements continue to redefine manufacturing processes across various sectors. In line with this trend, a groundbreaking technology has emerged in the foundry industry, promising unprecedented efficiencies and environmental benefits. This revolutionary induction technology, developed and commercialized by a pioneering industry leader, is set to transform the landscape of foundry operations worldwide.Background:The foundry industry has traditionally relied heavily on fossil fuel-powered furnaces to melt metal alloys for casting processes. Though effective, these traditional methods are environmentally taxing, generating significant greenhouse gas emissions and consuming large quantities of non-renewable resources. With growing concerns over climate change and sustainability, there has been a pressing need for forward-thinking solutions that address these issues without sacrificing operational efficiency.Induction Technology: A Paradigm ShiftEnter the groundbreaking induction technology, a transformative breakthrough that promises to redefine the foundry sector. The technology enables the melting of metal alloys through electromagnetic induction, rather than relying on conventional fossil fuel heating sources. This process significantly reduces the carbon footprint of the foundry industry, making it more sustainable and environmentally friendly.Induction Foundry: Leader in Revolutionizing Casting ProcessesOne prominent industry player at the forefront of this transformation is Induction Foundry (name removed). As a leading innovator and manufacturer of induction equipment, the company has played a pivotal role in driving the adoption of this game-changing technology. By combining expertise in metallurgy, engineering, and sustainable practices, Induction Foundry has introduced a range of highly efficient induction furnaces and equipment that have garnered worldwide acclaim.Increased Efficiency and Cost SavingsInduction Foundry's cutting-edge induction furnaces boast several advantages over conventional melting techniques. Firstly, the technology offers unparalleled energy efficiency, significantly reducing operating costs compared to traditional furnaces. Induction furnaces achieve optimal melting temperatures faster, resulting in shorter cycle times, increased productivity, and reduced energy consumption. The electromagnetic induction process also allows more precise temperature control, ensuring consistent casting quality and minimizing material waste.Environmental Sustainability at the CoreInduction Foundry's environmentally conscious equipment aligns well with the global sustainability movement. By eliminating fossil fuel combustion, the company's induction furnaces minimize emissions, improve air quality, and help combat climate change. Additionally, the induction process generates significantly less waste compared to traditional methods, as it avoids the need for refractory materials. These sustainable features have positioned Induction Foundry as a responsible industry leader, garnering acclaim and recognition from environmental organizations.A Future-Proofed Foundry IndustryWith environmental regulations becoming increasingly stringent and consumers demanding products manufactured through sustainable processes, the foundry industry must adapt rapidly. Induction technology offers the perfect solution - a highly efficient, sustainable, and cost-effective alternative to conventional melting processes. By embracing induction technology, foundry operators can modernize their facilities, enhance operational efficiency, and gain a competitive edge in the market.Global Adoption and Growth PotentialInduction Foundry's induction furnaces have witnessed substantial adoption across the globe. Foundries in various industries, such as automotive, aerospace, and machinery manufacturing, have implemented this transformational technology. The positive feedback and success stories from early adopters have further accelerated the growth potential of the induction foundry industry.Conclusion:As the global focus on sustainability intensifies, the foundry industry must embrace new and innovative technologies to stay ahead of the curve. Induction Foundry's pioneering induction technology presents a transformative opportunity for foundries worldwide to enhance productivity, reduce costs, and minimize environmental impact. With a growing customer base, Induction Foundry's induction furnaces are setting new benchmarks for the foundry industry while paving the way for a more sustainable future.
Top Coreless Induction Melting Furnace Suppliers in China
China Coreless Induction Melting Furnace Suppliers Revolutionize the Metal Casting IndustryWith its vast expertise and groundbreaking innovations, China's coreless induction melting furnace suppliers have become frontrunners in the metal casting industry. Advancements in technology, coupled with the dedication of these suppliers, have revolutionized the way metal is melted and cast, bringing unmatched efficiency and quality to the process.The coreless induction melting furnace is a critical tool used in the metal casting industry. It is used to melt various metals such as iron, steel, copper, and aluminum, which are then formed into different shapes and structures. Traditionally, metal casting relied on fossil fuel-powered furnaces, which posed environmental concerns and were prone to inconsistencies in melting. However, with the introduction of coreless induction melting furnaces, these challenges have been mitigated.China's coreless induction melting furnace suppliers, renowned for their commitment to excellence, have developed state-of-the-art equipment that addresses key issues faced in the industry. These suppliers offer advanced furnaces that utilize electromagnetic induction to achieve efficient and precise melting, resulting in superior quality castings.One of the key advantages of coreless induction melting furnaces is their ability to provide a cleaner and more environmentally friendly melting process. Unlike traditional fuel-powered furnaces, these induction furnaces operate using electricity, which significantly reduces harmful emissions. This not only benefits the environment but also complies with stricter regulations on emissions imposed by governments worldwide.Moreover, coreless induction melting furnaces offer enhanced control and accuracy in the melting process, resulting in consistent and homogenous molten metal. The advanced electromagnetic technology employed in these furnaces allows for better temperature control and even distribution of heat throughout the entire melting chamber. This ultimately leads to the production of high-quality castings with improved mechanical properties and reduced defects.To meet the growing demand for coreless induction melting furnaces, China's suppliers have diligently expanded their production capacities. They have invested heavily in research and development to enhance the performance and efficiency of their furnaces. These efforts have helped establish China as a global leader in the production of coreless induction melting furnaces, with a robust supplier network that provides reliable and cutting-edge equipment to various industries worldwide.The success of China's coreless induction melting furnace suppliers can be attributed to their continuous drive for innovation. These suppliers consistently adapt and improve their furnaces to cater to the evolving needs of the metal casting industry. They actively seek feedback from customers and collaborate with industry experts to identify areas for improvement. This customer-centric approach has earned them a reputation for delivering highly reliable and efficient furnaces that offer excellent value for money.In addition, China's coreless induction melting furnace suppliers prioritize customer support and after-sales services. They provide comprehensive technical assistance, training, and maintenance support to ensure long-term satisfaction and maximum uptime for their customers. This commitment to excellent customer service has resulted in enduring relationships with clients and a loyal customer base.Looking ahead, China's coreless induction melting furnace suppliers continue to innovate and push the boundaries of technology in the metal casting industry. They remain focused on developing furnaces that are even more energy-efficient, environmentally friendly, and capable of melting a wider range of metals. Through their dedication, these suppliers are revolutionizing the metal casting process, enabling manufacturers to achieve higher productivity, exceptional quality, and sustainable operations.In conclusion, China's coreless induction melting furnace suppliers have emerged as key players in the metal casting industry, offering advanced equipment that revolutionizes the melting and casting process. Their commitment to innovation, customer satisfaction, and environmental sustainability makes them invaluable partners to manufacturers worldwide. As they continue to push the boundaries of technology, these suppliers are set to reshape the future of metal casting with their cutting-edge furnaces.
Discover the Latest Innovation in High-Quality Smelting Equipment
Title: Advanced Smelting Equipment Revolutionizes Company OperationsIntroduction:In a significant milestone for the manufacturing industry, a leading company in the field of smelting equipment has developed state-of-the-art machinery that is set to revolutionize the way companies carry out their smelting processes. Fueled by years of research and development, this cutting-edge equipment promises to enhance efficiency, productivity, and sustainability, presenting a new era for companies engaged in metal refining and other related activities. With an unwavering dedication to innovation, this company is making strides to reshape the industry landscape, offering businesses a competitive edge in the global market.I. Smelting Equipment's Technological Breakthrough:The newly developed smelting equipment, (remove brand name), represents a technological breakthrough for the industry. It incorporates advanced features and functionalities that streamline the smelting process, offering significant advantages to companies looking to optimize their operations. With an emphasis on efficiency and sustainability, this cutting-edge equipment is built to minimize energy consumption, reduce waste, and enhance the overall quality of the end product.The equipment's intelligent monitoring system ensures accurate temperature control, resulting in improved metal purity and reduced material losses. Additionally, the incorporation of automation technology not only minimizes the risk of human error but also enables the equipment to operate continuously for extended periods, significantly boosting production capacity.II. Enhanced Safety Measures:In line with industry demands for improved safety standards, the smelting equipment integrates comprehensive safety measures to protect both operators and the environment. The introduction of advanced sensors and alarms monitors critical parameters such as temperature, pressure, and gas concentration, promptly alerting operators to any potential risks or deviations. This proactive approach ensures a safer working environment and minimizes the likelihood of accidents.Furthermore, the equipment is designed with a state-of-the-art waste gas treatment system, effectively reducing emissions and adhering to stringent environmental regulations. By minimizing environmental impact, companies utilizing this advanced smelting equipment demonstrate their commitment towards sustainable manufacturing practices.III. Improved Cost-efficiency and Resource Optimization:With the new smelting equipment, companies can expect significant cost savings and resource optimization. The integration of precision control mechanisms maximizes the extraction of valuable metals from raw materials, reducing the amount of waste generated. This enhanced efficiency not only reduces material costs but also contributes to a more sustainable use of available resources.Moreover, the equipment's intelligent energy management system optimizes power consumption by regulating energy output during peak and low demand periods. This results in reduced energy bills for companies and a smaller overall carbon footprint, aligning with contemporary goals of environmental stewardship.IV. Market Competitiveness and Global Reach:With the adoption of this advanced smelting equipment, companies gain a competitive edge in the global market. The increased efficiency and improved product quality achieved through the equipment's cutting-edge technology allow businesses to meet customer demands more effectively and respond to market fluctuations with greater agility.By embracing sustainability and incorporating state-of-the-art equipment into their manufacturing processes, companies utilizing this smelting equipment can market their products as environmentally responsible and gain a competitive advantage in increasingly eco-conscious markets.V. Company's Commitment to Innovation:The development and launch of this breakthrough smelting equipment signify the company's commitment to ongoing innovation and industry leadership. With a dedicated research and development team, the company continues to leverage the latest technology to enhance its offerings, meeting the evolving needs of the industrial sector.As a leading provider of smelting equipment, the company remains focused on providing comprehensive solutions to its customers and contributing to the advancement of the manufacturing industry as a whole. Their dedication to innovation ensures that businesses can achieve improved operational efficiencies, environmental sustainability, and increased profitability.Conclusion:The unveiling of advanced smelting equipment by (remove brand name) marks a revolutionary turning point for manufacturing companies engaged in metal refining. With enhanced efficiency, safety, and sustainability, this cutting-edge equipment empowers businesses to optimize their smelting processes, reduce costs, and gain a competitive edge in the global market. As the company continues to spearhead innovation, the future of the smelting industry looks increasingly promising, ushering in a new era of heightened performance and environmental responsibility.
Exploring the Efficiency of Automatic Melting Furnace Factories
As industrial techniques continue to evolve, companies in the manufacturing sector are always on the lookout for new and innovative ways to improve their processes. One of the latest advancements to hit the market is the automatic melting furnace. These furnaces have been revolutionizing the way that manufacturers in a range of industries melt metals and alloys.Automatic melting furnaces are specifically designed to heat heavy metals and alloys to extremely high temperatures in order to melt them down into a liquid form. This is a critical step in many manufacturing processes, particularly for industries such as automotive and aerospace, where the use of metals and alloys is necessary for producing high-performing components.In order to meet the growing demand for this cutting-edge technology, several automatic melting furnace factories have popped up worldwide. While each factory may have its own unique approach to creating these furnaces, they all share a common goal: to produce a product that is efficient, reliable, and cost-effective.One such factory, which I won't name due to the anonymity clause, has quickly become a leader in the industry. Founded several years ago, they specialize in the production of high-quality automatic melting furnaces that are specifically designed to meet the unique needs of their clients.Unlike traditional furnaces that require a great deal of manual labor to operate, automatic melting furnaces utilize advanced automation technology to carry out their functions. This not only makes them much more efficient, but it also reduces the need for labor, resulting in significant cost savings for manufacturers.Moreover, these furnaces are equipped with a range of safety mechanisms to prevent accidents and ensure smooth operation. From automatic temperature controls to built-in alarms and emergency shut-off switches, manufacturers can rest assured that their workers and equipment are protected at all times.But perhaps the most impressive aspect of this company's automatic melting furnace line is their customizability. With their team of experienced engineers and technicians, they are able to work closely with clients to develop furnaces that are tailor-made for their individual needs.From the size and capacity of the furnace to the specific automation features and safety mechanisms required, everything can be designed to meet the unique requirements of any manufacturing process. This level of customization is crucial, considering that every client has different needs and expectations when it comes to their manufacturing process.Overall, the rise of automatic melting furnaces is a testament to the constant evolution of industrial technology. As manufacturers continue to seek out ways to improve their processes, it is inevitable that more factories will begin to specialize in this cutting-edge technology. With its ability to streamline operations, reduce costs and improve safety, the automatic melting furnace is poised to become a staple in the manufacturing industry for many years to come.
How to Choose the Right Supplier for Your Induction Crucibles
China's Leading Induction Crucible Supplier Showcases Unparalleled Quality and Innovation in the Metal IndustryChina, known for its stellar manufacturing prowess, has once again taken center stage in the metal industry with its leading Induction Crucible Supplier (name redacted). This company has emerged as a pioneer in the production and supply of high-quality induction crucibles, catering to the varying needs of their global clientele. With a rich history of innovation and a commitment to excellence, (name redacted) continues its journey of providing state-of-the-art solutions to its customers.Established in China, (name redacted) has established itself as a formidable force in the metal industry. The company utilizes cutting-edge technology, combined with a team of experienced professionals, to deliver top-notch induction crucibles. Their unwavering dedication to quality has positioned them as the go-to choice for businesses seeking reliable and efficient crucibles worldwide.One of the primary factors that sets (name redacted) apart from its competitors is its unwavering commitment to innovation. The company recognizes the importance of staying ahead of the curve in an ever-evolving industry. By investing heavily in research and development, (name redacted) consistently introduces groundbreaking designs and advanced materials to revolutionize the crucible manufacturing process.The induction crucibles offered by (name redacted) are carefully engineered to withstand extreme temperatures, ensuring optimal performance and durability. These crucibles are designed to cater to a wide range of industries, including foundries, metal casting plants, and heat treatment facilities. Whether it is ferrous or non-ferrous metals, (name redacted) promises to deliver crucibles that exceed expectations, meeting the specialized needs of their discerning clientele.In addition to their commitment to quality, (name redacted) also emphasizes environmental sustainability. By employing eco-friendly practices throughout their operations, the company aims to minimize its carbon footprint. Their crucibles are manufactured using recycled materials wherever possible, showcasing their dedication to green manufacturing practices.With a robust and efficient supply chain, (name redacted) ensures that their products are available to customers across the globe. By forging strategic partnerships and leveraging their extensive network, the company minimizes lead times and ensures timely delivery to their valued clientele. This commitment to customer satisfaction has earned (name redacted) a reputation for reliability, cementing their status as a leading supplier in the inductions crucible market.The success of (name redacted) can also be attributed to their customer-centric approach. The company understands that every client has unique requirements and works closely with them to provide tailored solutions. By leveraging their technical expertise and industry knowledge, (name redacted) assists customers in selecting the ideal crucibles for their specific applications, optimizing efficiency and cost-effectiveness.(name redacted) firmly believes in building long-term relationships with their customers. They provide comprehensive after-sales support, ensuring that their clients receive the necessary guidance and assistance to maximize the lifespan and performance of their purchased crucibles. This commitment to customer care has garnered them a loyal customer base who value the company's dedication to their success.Looking to the future, (name redacted) aims to continuously push the boundaries of innovation while maintaining their unwavering commitment to quality and sustainability. By staying at the forefront of technological advancements, the company envisions a future where their crucibles will play an even more significant role in shaping the metal industry.In conclusion, China's leading Induction Crucible Supplier, (name redacted), has established itself as a key player in the international metal industry. Their dedication to innovation, commitment to quality, and unmatched customer support set them apart from the competition. As the company continues to expand its global presence, (name redacted) is poised to revolutionize the way industries approach metal casting and heat treatment processes.
Discover the Advantages of Aluminum Melting Furnaces
Title: Innovation Meets Efficiency: Introducing the Cutting-Edge Melting Furnace AluminumIntroduction (100 words):In today's rapidly evolving manufacturing landscape, efficiency and innovation are crucial elements for businesses to stay ahead of the competition. With this in mind, we are excited to introduce the latest breakthrough in metalworking technology – the groundbreaking Melting Furnace Aluminum. This advanced furnace model, developed by a renowned industry leader, offers an unparalleled combination of efficiency and performance. By revolutionizing the aluminum melting process, this state-of-the-art furnace is set to transform the manufacturing industry, helping companies reduce costs, enhance productivity, and maximize profitability.Body:1. Background and Development (100 words):Developed by a team of expert engineers and metallurgical specialists, the Melting Furnace Aluminum was designed with a focus on meeting the growing demand for efficient metal melting solutions. The development process involved extensive research and development, drawing upon decades of experience in the industry. The goal was to create a furnace capable of delivering consistent results, streamlining operations, and minimizing energy consumption.2. Features and Benefits (200 words):The Melting Furnace Aluminum boasts several revolutionary features that make it stand out from its competitors. Firstly, its superior insulation system ensures exceptional energy efficiency, significantly reducing operating costs and environmental impact. The furnace incorporates advanced temperature control mechanisms, allowing for precise and uniform heat distribution, resulting in optimal melting efficiency. This enables manufacturers to achieve higher productivity rates, minimize metal loss, and improve overall product quality.Furthermore, this innovative furnace utilizes cutting-edge automation technology that simplifies operation and reduces the need for manual intervention. The user-friendly interface allows operators to control and monitor the melting process remotely, enhancing safety and easing maintenance procedures. Additionally, the Melting Furnace Aluminum is equipped with state-of-the-art filtration systems, efficiently removing impurities and contaminants from the molten metal, resulting in a cleaner and higher-quality final product.3. Increased Productivity and Cost-Efficiency (200 words):The introduction of the Melting Furnace Aluminum promises to revolutionize metalworking processes by significantly increasing productivity while reducing costs. With its advanced features and capabilities, manufacturers can expect streamlined operations, reduced setup times, and overall higher efficiency.The furnace's rapid heating capabilities enable quicker melting cycles, minimizing downtime and increasing production output. Due to its precise temperature control, industries can achieve consistent results, reducing scrap rates and enhancing the yield of the melting process. Additionally, the reduction in energy consumption provided by its superior insulation system translates into substantial cost savings.4. Environmental Sustainability (150 words):As sustainability continues to gain importance in various industries, the Melting Furnace Aluminum emerges as a key player in supporting environmentally conscious manufacturing practices. Its energy-saving features, such as the efficient insulation system, contribute to a reduced carbon footprint. The optimized filtration system not only enhances product quality but also minimizes waste generation by filtering impurities from the molten metal, promoting a clean and sustainable production process.Conclusion (150 words):The introduction of the Melting Furnace Aluminum presents a turning point in the metalworking industry, as it combines cutting-edge technology, enhanced efficiency, and a commitment to environmental sustainability. This advanced furnace model promises to revolutionize the way metal is melted, leading to increased productivity, improved cost-efficiency, and superior product quality.With its state-of-the-art features and innovative design, the Melting Furnace Aluminum is set to become an indispensable tool for manufacturers seeking to streamline their operations, boost profitability, and reduce their environmental impact. As the demand for high-quality, energy-efficient metal melting solutions continues to grow, this groundbreaking furnace is poised to reshape the manufacturing landscape, setting new standards for excellence and innovation.
Innovative Induction Copper Melting Furnaces Now Available for Industrial Applications in China
China Induction Copper Melting Furnace Factory, one of the leading manufacturers in the industry, is keenly focused on revolutionizing the copper melting process. With their exceptional expertise and state-of-the-art technology, the company aims to redefine efficiency, precision, and eco-friendliness in the melting furnace industry. Their commitment to innovation and customer satisfaction has earned them a prominent position in the market.The China Induction Copper Melting Furnace Factory sets itself apart from competitors with its cutting-edge induction heating technology. This technology allows for a highly efficient and precise melting process, reducing energy consumption and ensuring minimal heat loss during production. By utilizing electromagnetic induction to generate heat directly within the material being melted, these furnaces offer unparalleled temperature control and uniformity.In addition to its advanced technology, the factory also places great emphasis on environmental sustainability. The China Induction Copper Melting Furnace Factory is fully aware of the impact of industrial processes on the environment, and has implemented various measures to reduce its carbon footprint. For instance, they have developed energy-saving systems that effectively minimize power consumption, resulting in reduced greenhouse gas emissions. This commitment to eco-friendliness not only benefits the environment but also helps businesses lower their operational costs.Furthermore, the China Induction Copper Melting Furnace Factory is deeply committed to providing top-notch customer service and support. With a team of highly skilled engineers and technicians, they offer comprehensive assistance from installation to maintenance. The company understands the importance of a reliable and efficient melting furnace in the production process. Therefore, they make it a priority to ensure that their clients receive the best possible service and prompt technical support whenever required.The factory's dedication to quality is evident in its rigorous testing and quality control procedures. Each furnace undergoes thorough inspection and testing before delivery, ensuring that it meets the highest industry standards. This attention to detail guarantees that customers receive a durable and high-performance product that will withstand the demands of continuous use.China Induction Copper Melting Furnace Factory's clientele spans across various industries, including metal processing, foundries, and recycling facilities. Their furnaces are widely used for melting copper and its alloys, providing an essential tool for these industries’ operations. The factory's ability to cater to various business requirements has contributed to its growing reputation as a reputable and reliable melting furnace manufacturer.Looking ahead, the China Induction Copper Melting Furnace Factory plans to continue its commitment to innovation and technological advancement. By staying at the forefront of industry trends and continuously updating their product offerings, they aim to provide customers with cutting-edge solutions for their copper melting needs. Through ongoing research and development, the company strives to enhance their furnaces' efficiency, performance, and sustainability, solidifying their position as an industry leader.In conclusion, the China Induction Copper Melting Furnace Factory is a standout player in the melting furnace industry. With its advanced technology, commitment to eco-friendliness, and dedication to customer satisfaction, the factory has earned its reputation as a reliable and innovative manufacturer. As they continue to evolve and improve their product offerings, they are poised to remain at the forefront of the industry, shaping and revolutionizing the copper melting process.
Massive Industrial Smelting Furnaces Boosting Metal Processing Efficiency
Recently, a large smelting furnace (brand name removed) has been introduced by one of the leading companies in the industry. With its advanced technology, this furnace has the potential to revolutionize the smelting process, making it easier, more efficient, and environmentally friendly.The large smelting furnace is capable of melting and refining a variety of metals, including copper, aluminum, zinc, and lead. It is particularly suitable for the production of high-quality metals, which are used in a wide range of applications such as construction, electronics, and automotive manufacturing.The furnace boasts of advanced features that set it apart from traditional furnaces. Its unique design allows for faster heating and cooling times, reducing the overall processing time significantly. Additionally, the furnace's digital controls ensure that the temperature and other parameters are accurately maintained, leading to a more precise and consistent product.Another key benefit of the furnace is its energy efficiency. By using state-of-the-art insulation and heat recovery systems, the furnace can operate at a much lower energy consumption than similar furnaces in the market. This translates to lower production costs, as well as reduced carbon emissions.The company behind the large smelting furnace is a well-established player in the industry, known for its cutting-edge technology and innovative solutions. With over five decades of experience, the company has built a reputation for delivering high-quality products and exceptional customer service.According to the spokesperson of the company, "We are thrilled to introduce the large smelting furnace to the market. This furnace represents a significant advancement in the smelting process, and we believe it will bring substantial benefits to our customers. We are confident that the furnace's advanced features and energy efficiency will help our customers optimize their production processes and reduce costs. We are committed to providing the best possible product and support to our customers."The company has already received several inquiries and orders for the furnace, indicating a strong demand for this innovative technology. Many customers have expressed their excitement about the prospects of using the furnace to improve their production processes and enhance their competitive edge.One of the customers who has already ordered the large smelting furnace is a leading aluminum manufacturer. The company's spokesperson commented, "We are constantly exploring new technologies that can help us improve our production processes and reduce our environmental impact. The large smelting furnace fits perfectly into our vision, and we are excited to incorporate it into our operations. We believe this furnace will allow us to produce higher quality aluminum at a lower cost, while also reducing our carbon footprint."Overall, the large smelting furnace is set to make a significant impact on the metal industry, offering a faster, more precise, and more environmentally-friendly alternative to traditional smelting processes. With a strong demand from customers and the backing of a reputable company, this furnace is poised to become a game-changer in the industry.
China's Leading Electric Lead Melting Furnace Factories
China Electric Lead Melting Furnace Factories Boost Lead Recycling EffortsIn recent years, there has been a growing concern about the impact of lead on the environment and human health. Lead, a toxic heavy metal, can contaminate soil, water, and even air, posing significant risks to living organisms. In response to these concerns, China Electric Lead Melting Furnace Factories have made great strides in developing and manufacturing advanced lead melting furnaces that enable efficient lead recycling.China Electric Lead Melting Furnace Factories have been at the forefront of promoting sustainable practices in lead processing. By creating cutting-edge lead melting furnaces, these factories are providing an eco-friendly solution to the increasing demand for lead recycling. The advanced technology employed in these furnaces allows for better control and regulation of the melting process, resulting in higher purity lead and reduced emissions.Lead recycling plays a vital role in reducing environmental pollution and conserving natural resources. Through the use of electric lead melting furnaces, lead-acid batteries, which contain large amounts of lead, can be efficiently and safely recycled. The lead melting furnaces are designed to handle the specific requirements of lead recycling, ensuring the conversion of lead into reusable materials.Apart from environmental benefits, lead recycling also presents economic opportunities. The demand for lead is continuously increasing, driven by various industries such as automotive, construction, and electronics. By investing in advanced lead melting furnaces, China Electric Lead Melting Furnace Factories are not only fulfilling the need for lead but also contributing to the circular economy. These furnaces enable the extraction of lead from secondary sources, decreasing dependency on virgin raw materials and reducing production costs.Furthermore, China Electric Lead Melting Furnace Factories prioritize safety in their operations. The lead melting furnaces are equipped with advanced safety features and automated control systems, minimizing the risk of accidents and ensuring a safe working environment. The factories strictly adhere to international safety standards and regulations, guaranteeing that their products meet the highest quality and safety requirements.The company behind these innovative lead melting furnaces traces its origins back several decades. Established with the vision of providing sustainable solutions for lead processing, the company has grown into a prominent player in the industry. With a strong focus on research and development, they continuously strive to enhance their products' performance and efficiency.The commitment of China Electric Lead Melting Furnace Factories to sustainable lead recycling is commendable. By manufacturing state-of-the-art lead melting furnaces, they promote environmental protection, resource conservation, and economic growth simultaneously. Their efforts align with China's broader goals of transitioning towards a greener and more sustainable economy.Looking ahead, China Electric Lead Melting Furnace Factories plan to further expand their product lineup, catering to the evolving needs of the lead recycling industry. They intend to develop furnaces with even higher energy efficiency and lower emissions, ensuring that the recycling process becomes even more environmentally friendly.In conclusion, China Electric Lead Melting Furnace Factories are playing a significant role in advancing lead recycling efforts in China. Through the development and manufacturing of advanced lead melting furnaces, these factories enable the safe and efficient recycling of lead, reducing environmental pollution and conserving valuable resources. Their dedication to sustainability and commitment to producing high-quality and safe products make them a key player in the global lead processing industry.